"We kept some high-volume business as a result of the Ttarp press that we would have lost without it. There’s no doubt it paid for itself. It is a workhorse."
General Manager
Technical Converter | Colorado
Below is a quick specification summary on the belts that we provide with Ttarp’s Automatic Presses
1. Poly-Coated, .02” thickness, is the lowest cost and the least dense. This has a polyethylene coating on both sides. Foam and lighter density materials should be cut on this belt. It has a belt thickness tolerance of +/- .004”. Sold in 3000 linear foot rolls.
Stock roll widths [in]: 20, 28, 30, 35, 37, 38
2. Ttarp Hard Tan, .02” thickness, is an uncoated dense belt. Almost anything can be cut on it including difficult foams, rubber, plastic, carpet etc. It is hard and will have approximately 3X the life cycle vs. poly-coated. Thickness tolerance is +/- .004”. It has no coatings so is good for heat sealing. Sold in 1000 linear foot rolls.
Lab Tests to simulate hardness include the Mullen Burst (Tappi T 807) and Ring Crush (Tappi T 818) tests:
Poly-Coated: Mullen Burst = 187 outside, 205 inside Ring crush = 208 outside, 161 inside
Ttarp "Hard Tan": Mullen burst = 485 out, 488 in Ring crush = 314 out, 337 in
Stock Rolls widths [in]: 29, 30, 31, and 37”
3. Mylar Type A, .014” thickness, is uncoated and the densest cutting belt. This is ideal when an application includes kiss cutting. It has tight thickness tolerances of +/- .0005” and is harder than PSA liners. It is very hard so good for cutting difficult woven materials such as canvas, felt, stringy insulation materials like thinsulate, etc. It can be good for heat sealing with an upper heat platen due to structural integrity at high temperatures. Sold in 200 linear foot rolls.
Stock roll widths [in]: 12, 15, 18, 20, 24, 28, 30, 31, 35, 36, 37, and 60
4. Urethane belt, often .125” thick, is the most expensive belt (lasts longer). Used with both knife and serrated edge rule. Due to it’s relative softness and thickness tolerances, it is not consistent enough for high quality – volume kiss cutting. On the Ttarp Automatic press, an optional upgrade is required to increase the size of drive servo motor, upgrade to the drive roller, upgrade to the belt tracker, upgrade to the belt tensioner, etc. The weight of the cutting belt is 4X the other belts driving the size increases mentioned above. This belt is typically welded on site by an outside service at the belt joint versus the use of simple shipping tape for the other Ttarp supplied belts.
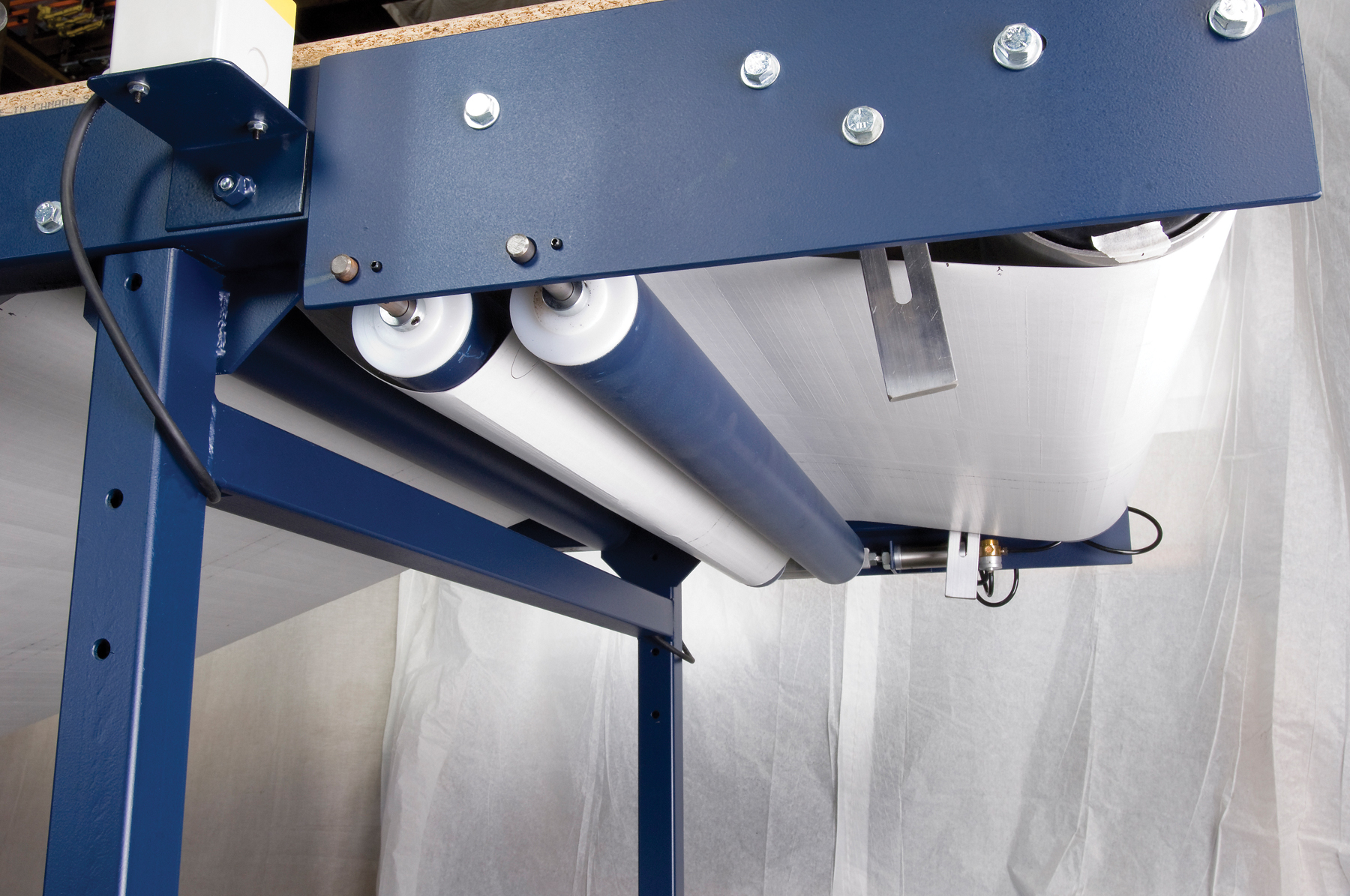
“This is the most reliable machine on the planet.”
Manufacturing Engineer
Sample Carpet Converter | Georgia
“Getting the Ttarp press up and running was smooth. It took three hours from the time of arrival. I didn’t expect that.”
Manufacturing Engineer
Technical Converter | Colorado