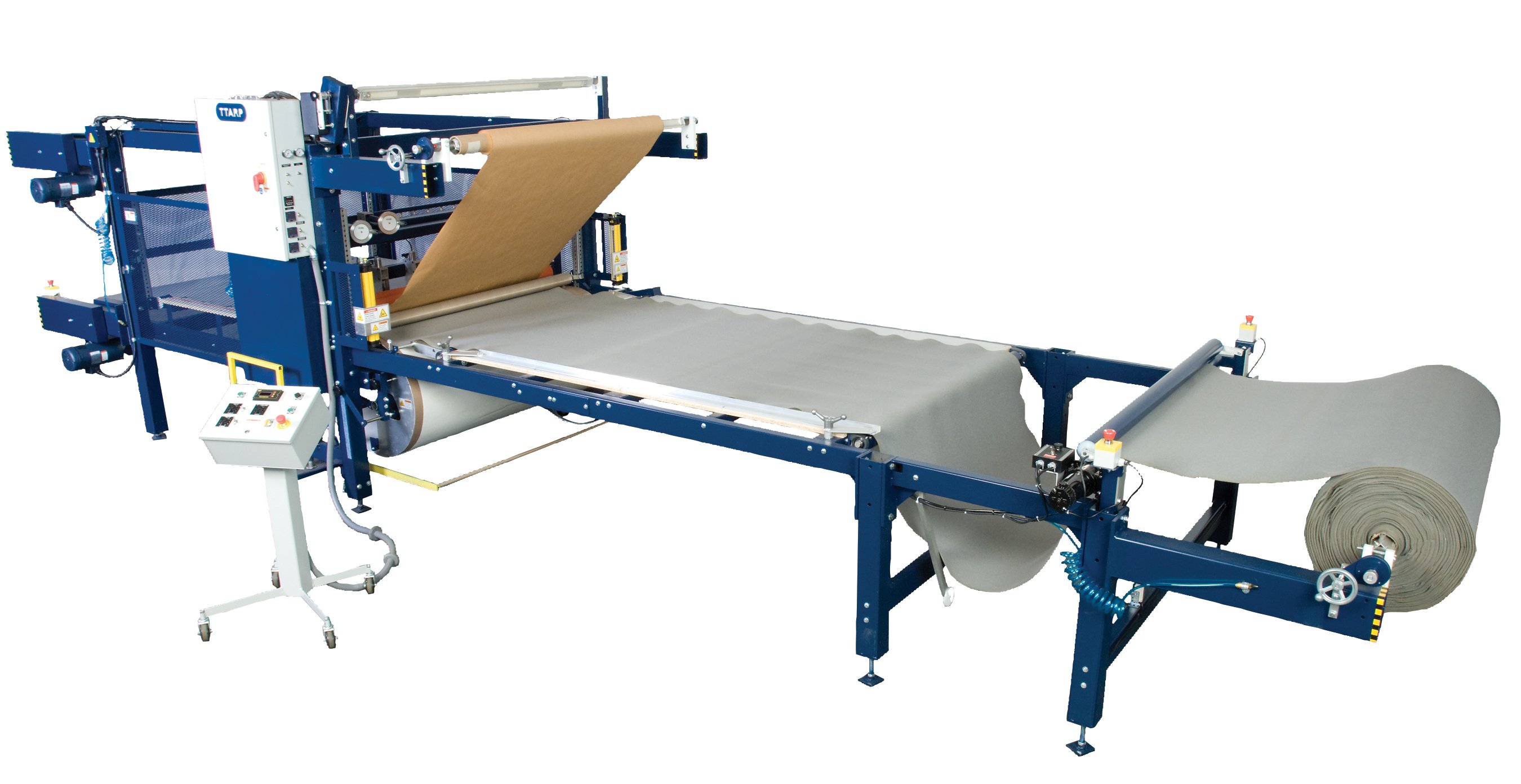
Standard Features for 60” Heat Laminating Systems
Ttarp designs and manufactures 60” heat laminating systems to laminate, slit and rewind heat-activated or cold-bonding pressure-sensitive adhesive (PSA) products. Ttarp laminators are available with an extensive range of options to customize your system.
Download Specification Sheet:


Option A
- 3” dia. airshaft with brake/tracking
- 36” roll diameter max., 200lb standard
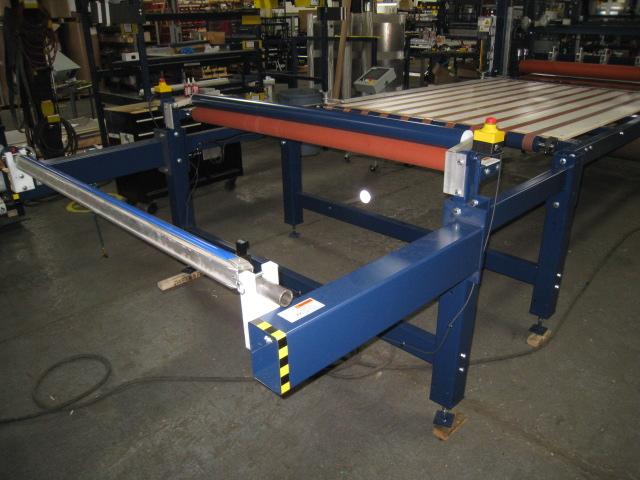
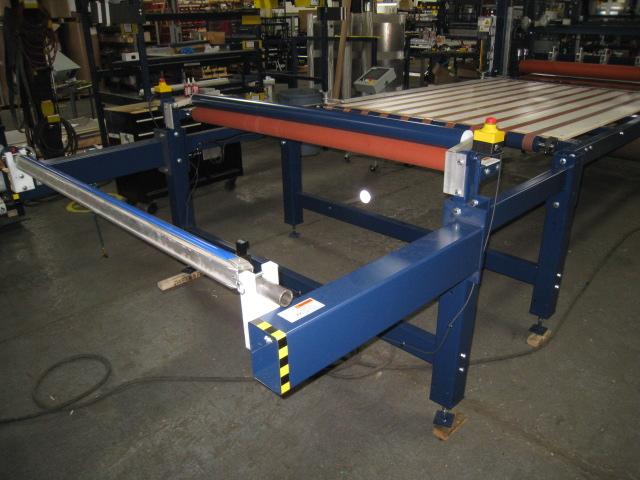
Option B & Option C
- Option B : 8’ Powered infeed conveyor table with belts
- “Feeds” material vs. Nip Rollers pulling material by nip rollers
- Provides more time for material relaxation
- Plank feeding
- Option Y : Infeed conveyor table is independently driven from pinch rollers via second servo drive and PLC control.
- Allows PSA Lamination without stretch across multiple materials, thicknesses, and densities.
- Real time & incremental adjustment. Optimized value saved in PLC recipe library
- Option C : Material Relaxation loop sensor (between orange roller and table)
- Relaxes material from over tension inbound rolls
- 3” dia. airshaft
- 48” roll diameter max. , 200lb standard, Options for 300lb and 750lb
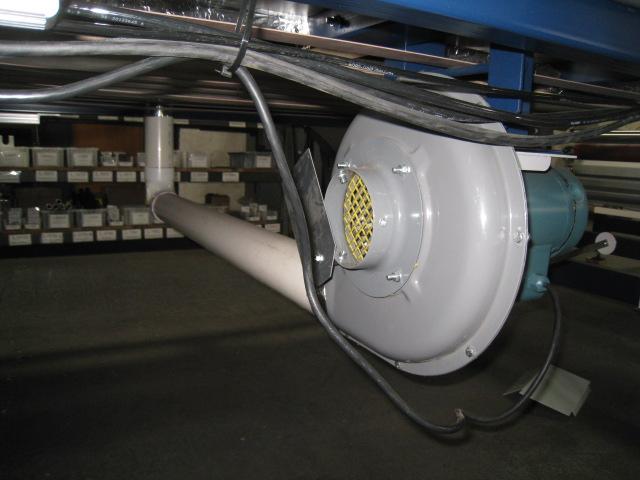
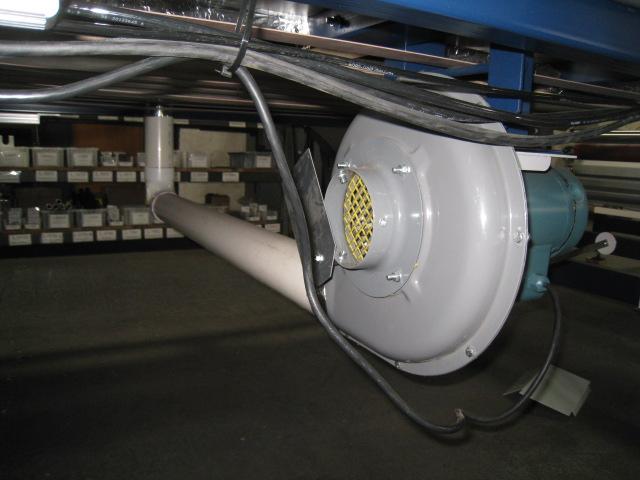
Option B1
- Positive pressure air blows through conveyor table to relax material prior to lamination
- Independent on/off switch with power tied into main panel







Option J
- Pneumatic Material Lifts for both the infeed (J2) and outfeed (J1) of the machine
- 48” roll diameter max., 300lb standard
Drops/lifts rolls to floor
Horizontal support designed not to drop all the way to floor. No toe pinch point.
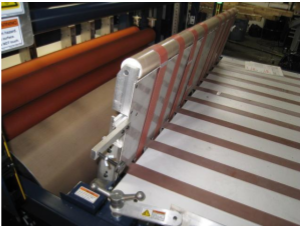

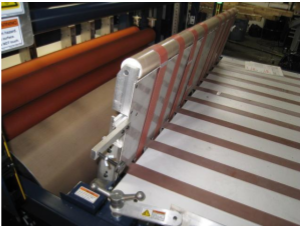

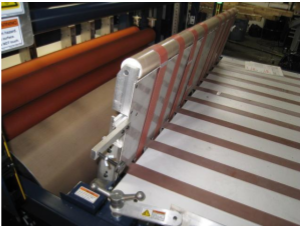

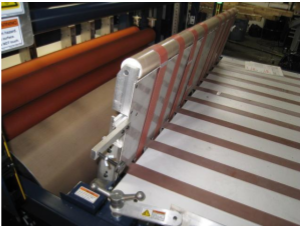
Option Z
- Infeed conveyor bridge for thin sheet materials
- Adjustable pitch and length for optimal material entry
- Prevents friction induced waves on bridge and early contact with PSA


Option L3
- Automated sheeting saw for cutting to length: Roll to sheet applications
- Accurate sheet lengths to +/- 1/8” (15-20 fpm operating speed)
- Adjustable traverse speed and RPM via touchscreen
- Automated, upstream, pneumatic clamp bar for material rigidity
- Adjustable travel limit switches for narrow width materials
- Cuts in both directions


Option T
- Similar to option L3, automated cutting to length. The pneumatic cutting head module is designed to be interchangeable with the motorized spinning blade of option L3. Option T is a pneumatic pressure crush cut against a hardened anvil surface
- Air pressure from plant is modulated with external gauge and regulator
- Application: thin rubbers, thin neoprene, thin silicone


Option S
- Bottom Driven Roller upstream of L3 Cutoff saw with gap control
- Provides drive for thin material to prevent waves prior to the cutoff saw
- Provides stability for material being slit to width and cut to length that tends to spaghetti downstream on slitting


Option R
- Same as Option S above with driven bottom roller and upper gravity roller vs. gap setting


Option N & Option B (outfeed table)
- Option-N : Outfeed, upper, secondary rewind – torque wind up
- 3” airshaft
- 48” roll diameter max., 200lb standard, Option for 300lb
- Option-B : Outfeed 8’ table
- Conveyor carries thin sheets out of the automated cut off saw for operator or another conveyor
- An outfeed table (no conveyor) for stiffer planks being sheeted from a roll serves as a working table to stack sheets on pallet


Option E
- Powered rewind on adhesive cart for PSA with two liners
- Positionally interchangeable with the upper, secondary let-off, option A
- 3” airbar, 200lb
- 1/8hp, 110v inline quick disconnect plug in to main panel supplied







Option E-HD
- Heavy Duty Cast Liner Rewind cart
- Mounted to the infeed of the machine and designed to automatically remove and rewinding cast liners from substrates prior to lamination. Allows shrinkage of cast substrates before adhesive liner locks stretch into place. (ie. PVC, Poron, etc.)
- 3” airbar, 200lb
- 1/3hp, 110v inline quick disconnect plug in to main panel supplied


Option W
- Foot Pedal
- Typical application is for hands free, single man, start/stop operation of the primary rewind for shrink wrapping master rolls
- Less frequent application is for hands free, start/stop operation of infeed conveyor table when loading planks from a pallet
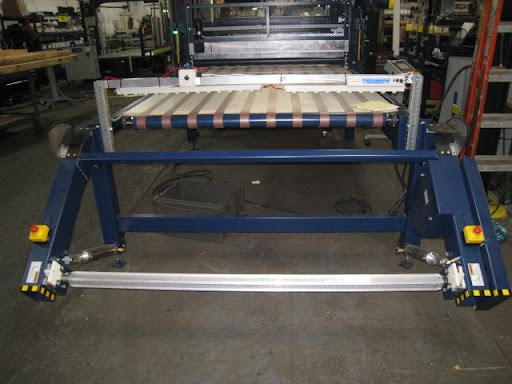


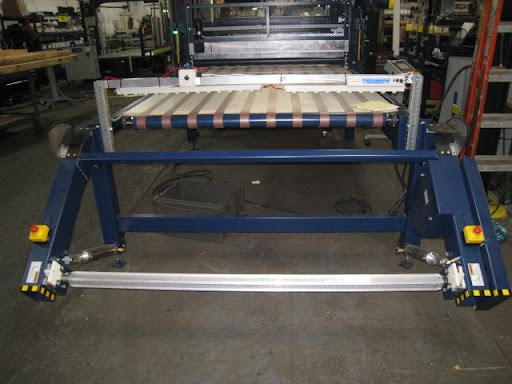


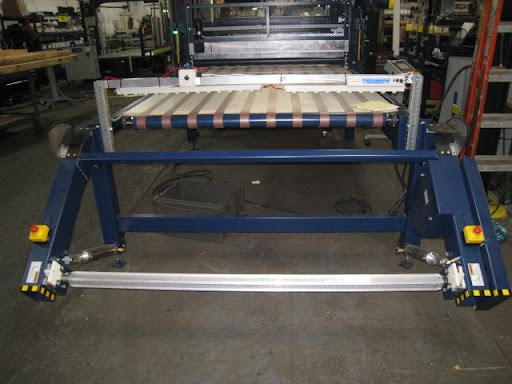


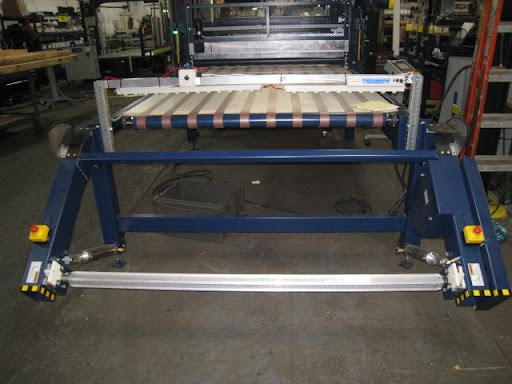
Misc. Options
- Anti-static systems, corona treatment, constant tension rewind – magnetic particle clutches, etc.
- Call us at (716-894-5613)
Option K
- Option-Rotary Blade Assembly (2 hp motor, 5 PCs, 7 1/2 blades); Includes Outfeed Light Curtain